Understanding ESD in Manufacturing: Causes, Effects and Prevention.
- vidith cc
- Apr 7
- 4 min read
What is ESD?
Electrostatic Discharge (ESD) refers to the sudden transfer of static electricity between two objects that have different electrical charges. This discharge often occurs when two materials come into contact and then separate, causing an imbalance of electrical charges. In manufacturing environments, particularly those dealing with sensitive electronic components, ESD can pose a significant risk. The unexpected transfer of static electricity can lead to severe damage to these delicate components, affecting the quality and reliability of the products being manufactured.
Why is ESD a Problem in Manufacturing?
ESD can wreak havoc on a wide range of electronic devices and components, even when the discharge is too small to be felt by humans. A seemingly harmless spark of static electricity can destroy sensitive circuitry, leading to product failures, malfunctions or even complete system breakdowns. The impact of ESD is not just limited to physical damage to electronic components. It can also result in reduced reliability, performance issues, increased operational costs due to rework or scrap and ultimately affect the bottom line of manufacturing businesses.
Industries that rely heavily on the assembly of electronics, semiconductors and Printed Circuit Boards (PCB's) are particularly vulnerable to the risks associated with ESD. These industries use highly sensitive devices, making the need for effective ESD protection even more crucial. Whether you’re assembling computers, smartphones or other electronic equipment, ensuring that your production line is free from ESD is vital to maintaining product integrity and minimizing risks. To mitigate these potential hazards, manufacturers must employ rigorous ESD protection strategies.
ESD Protection Measures
There are a variety of methods and specialized equipment that manufacturers can use to prevent and control ESD. By implementing the right protective measures, companies can safeguard their electronic components from the damaging effects of static electricity. Below are some of the most effective strategies for managing ESD:
1. ESD-Safe Workstations with Grounding Systems
ESD-safe workstations are designed with grounded surfaces and conductive materials that help dissipate static electricity safely. These workstations are crucial for assembly, testing, and repair operations, especially when dealing with static-sensitive components. Grounding systems ensure that any buildup of static electricity is safely discharged before it can cause damage.
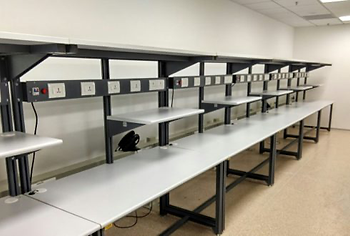
2. Anti-Static Mats and Wrist Straps
One of the most common ESD protection methods involves the use of anti-static wrist straps and mats. Workers who handle electronic components typically wear wrist straps that are connected to a grounding point. This ensures that any charge accumulated on the worker’s body is safely discharged before touching sensitive components. Anti-static mats, which are often placed on workbenches or floors, also provide a grounded surface to prevent the buildup of static electricity.

3. Ionizers for Static Neutralization
Ionizers are devices that emit balanced ions into the air, which helps neutralize any static charges present. Ionizers are particularly useful in environments where traditional grounding methods may not be feasible. For example, when grounding isn’t possible in specific areas of the factory, ionizers can be deployed to ensure that electrostatic discharge doesn’t compromise the integrity of electronic components.

4. ESD-Safe Packaging
In addition to on-site protection, manufacturers also need to consider the risks of ESD during transportation and storage. Sensitive components are often placed in ESD-safe packaging, such as static shielding bags, conductive boxes, or foam inserts. These packaging materials are designed to protect against electrostatic discharge during handling, shipping and storage.
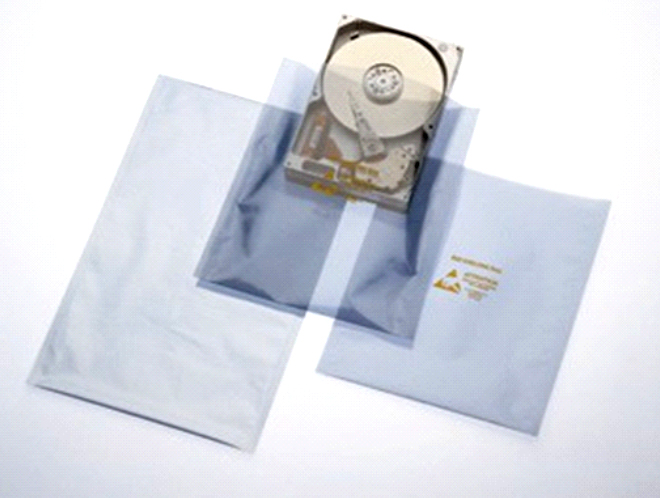
Best Practices for ESD Management
While using specialized ESD protection products is essential, manufacturers must also follow best practices to create a comprehensive ESD management system. Here are some key practices to implement:
1. Train Employees
Educating your staff about the risks of ESD and the best practices for handling electronic components is vital. Proper training ensures that everyone understands how to handle sensitive materials safely, reducing the risk of accidental discharge.
2. Regular Testing
Regular testing of your ESD protection devices and equipment is essential to ensure they remain effective. Routine checks can help identify any potential issues before they cause problems on the production floor.

3. Control Humidity
Static electricity tends to build up more readily in dry environments. Maintaining a relative humidity level between 40% and 60% in your manufacturing environment can help reduce the likelihood of static buildup, making it easier to control ESD.

4. Designate ESD-Controlled Areas
Clearly marked ESD-controlled areas are crucial for keeping sensitive components safe. Ensure that these zones are properly maintained, with signage and floor markings to remind employees to follow proper ESD protocols.
5. Implement ESD Audits
Conducting regular ESD audits helps identify potential risks and address them before they become problems. Audits can assess whether your ESD protection measures are being followed and whether they need improvement.
Conclusion
Controlling Electrostatic Discharge (ESD) in manufacturing environments is not just a preventive measure, but a necessary investment in the long-term quality and reliability of your products. By using ESD-safe workstations, anti-static tools, ionizers, and protective packaging, manufacturers can significantly reduce the risk of electrostatic discharge damage. In turn, this helps maintain product integrity, minimize costly defects, and enhance customer satisfaction.
Protect your sensitive components and ensure a smooth, seamless manufacturing process with reliable ESD solutions. Take a proactive approach to managing electrostatic discharge risks and explore our comprehensive range of ESD protection products to create a static-safe environment in your facility.
Comments